Mechanical Engineer, Manufacturing Engineer
Jason Moore
Testing/Results
Introduction: For the drivetrain on the RC car, a speed, assembly and disassembly, weight and volume test were performed. The requirements and parameters for this project included a speed of 20-25mph, a 5 minute assembly and disassembly time, a 3lb weight limit (of only drivetrain components) and a 6.5x3x3 volume. From initial calculations it was predicted that car would achieve at least 20mph, weigh less than 3lbs, fit within the required volume and be assembled and disassembled in less than 5 minutes.
Method/Approach: The resources needed to complete these test include tape, tape measure, stopwatch, simple hand tools such as hex keys, and a scale. The data was initially gathered on raw data sheets at the location of the test and then processed later in excel and organized into tables. These tests were fairly simple and no special tools or resources were needed for the test procedures. The procedures included gathering the appropriate supplies for the given test, perform the test, record the results and then clean up. The only operational limitations occurred with the speed test where the battery pack and motor were the biggest determinates of the actual speed of the car. There were some energy losses in the actual drivetrain itself as well. Due to the simplicity of these tests, there is no need for high precision or accuracy and nothing was recorded past 0.1 (units) and most weren’t recorded past the decimal. All of the tests were performed multiple times for accuracy however. The only data manipulated occurred with the speed test because it was recorded in feet/second and had to be converted to MPH which is, again, another simply manipulation.
Test procedures: To perform all four tests took 4-4.5 hours. The speed test took one hour, the assembly and disassembly tests took two hours and the weight and volume tests took a little over an hour to perform. The longest test being the assembly test because the drivetrain was repeatedly assembled and disassembled and each took roughly 5 minutes and each was repeated three times. All of the test were performed in Hogue hall where the resources were available. The following are the procedures for each of the 4 tests that were performed.
Speed: Hogue Hall, Fluke Lab:
-
Measure out a 20ft distance with a tape measure and put tape markers at 0ft and 20ft. Allow for 10ft before the 0ft marker location for acceleration.
-
Have one partner stand upstairs with a stopwatch, overlooking the 20ft distance.
-
Accelerate the RC car to a constant speed before the 0ft location.
-
Once car is at constant speed, record the time it takes for the car to span the 20ft distance.
-
Calculate the MPH that the car reached using the general equation Speed=distance/time and apply the proper conversions.
-
Repeat steps 3-5 five times while slowly increasing the speed until the car reaches at least 25MPH.
-
Measure and record in excel spreadsheet.
Assembly & Disassembly: Hogue Hall, Fluke Lab:
-
Start the timer and begin disassembly of the drivetrain.
-
Stop the timer when disassembly is complete.
-
Record time.
-
Reassemble drivetrain and record the time.
-
Stop the timer when reassembly is complete.
-
Record time.
-
Repeat 3-4 times and record data in excel spreadsheet and calculate the average time.
Weight: Hogue Hall, Fluke Lab:
-
Disassemble drivetrain assembly from chassis.
-
Weigh drivetrain 3-4 times for accuracy.
-
Record weights in table.
-
Calculate average.
Volume: Hogue Hall, Fluke Lab:
-
Measure overall height.
-
Measure overall width.
-
Measure overall length.
-
Calculate total volume.
-
Repeat 3-4 times for accuracy.
-
Record data in table.
The biggest risk concerned with these tests was time due to various deadlines that had to be met. The only safety concern is with the speed test. There was potential for it to hit someone at its max speed but since it didn’t reach 20 MPH this concern dissipated. The area was marked off just to be safe anyways. Another smaller risk was that some of the components could have been lost because they are so small and hard to handle (some parts being only 3mm in diameter). Because of this, extreme organization took place during the assembly and disassembly tests.
Deliverables: For the speed test, it was predicted to go about 20MPH (max speed) but after performing the test, the average speed was around 12MPH due to various losses in the drivetrain and the power supply. A bigger motor would be an economical and relatively easy solution to achieve the 20MPH requirement. The assembly and disassembly tests resulted in times under 5 minutes with disassembly taking 4:12 minutes (average) and assembly taking 4.58 minutes (average). The weight test also did well with the drivetrain weighing in at 2.67lb and the volume test resulted in a 6.2X3X2.8 in3 Volume. Overall the tests were considered a success other than the speed test. It’s worth noting that the speed test was based off the output RPM of the motor and the gear ratios in the reductions.
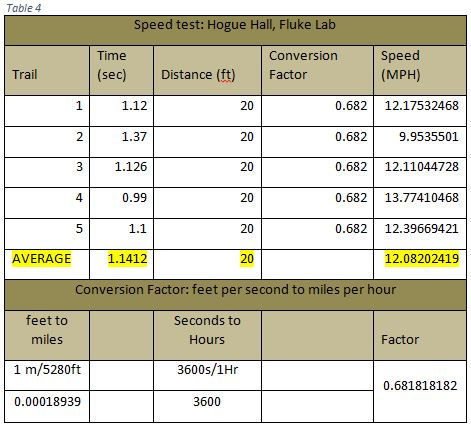


